Isocyanates and Polyols
Biomass Balance Approach
Saving valuable resources and reducing CO2 emissions:
BASF’s biomass balance approach (BMB) scores on both counts. The concept promotes the use of renewable raw materials in BASF’s Production Verbund and can be applied to most of the products in BASF’s portfolio, including our polyurethane base products, such as BASF isocyanates and polyols. They are marketed as our BMBcertTM portfolio.
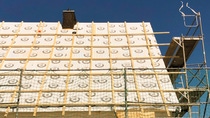
In a nutshell: the advantages of the biomass balance approach:
- 100% substitution of fossil raw materials with renewable resources in the value chain
- Significant reduction of the carbon footprint compared with conventional BASF products
- Drop-in solution: same quality and properties compared with conventional BASF products
- Available for a wide range of monomers. A list with the overview can be found here: Isocyanates / Polyols
- Biomass balance approach certified in accordance with recognized standards such as REDcert2
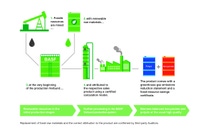
Certified renewable raw materials
In the biomass balance method, renewable raw materials such as bio-naphtha and biomethane derived from organic waste, agricultural products, or vegetable oils are used as a feedstock in the manufacture of basic chemical products. The proportion of bio-based raw materials is then allocated to specific sales products according to the certified method.
Independent certification
BASF has established a closed control chain that extends from the renewable raw materials used all the way to the end product. Independent certification confirms that BASF has replaced the required quantities of fossil resources with renewable feedstock for the biomass-balanced product sold. BASF’s monomers division has major sites and more than 200 products already RedCert2 or ISCC+ certified today. It aims to have additional sites certified in all regions and will continue to expand its portfolio of certified mass balanced products for its customers worldwide.
Would you like to find out more? Then watch our video on the BMB approach here.