Isocyanates and Polyols
Chemical Recycling (Depolymerization)
Did you know that around 40 million mattresses end up in landfills and incinerators in Europe every year? At the same time, valuable raw materials are consumed in the production of new flexible foam mattresses. Chemical recycling of mattresses can close the loop for flexible polyurethane foam. And this is how we at BASF Monomers are making a valuable contribution to sustainability.
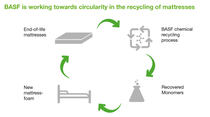
In a nutshell: the advantages of the ChemCycling® approach
- 100% substitution of fossil raw materials with recycled raw materials in the value chain
- Significant reduction of the carbon footprint compared with conventional BASF products
- Drop-in solution: same quality and properties compared with conventional BASF products
- Available for a wide range of monomers. A list with the overview can be found here: Isocyanates
- ChemCycling® approach certified in accordance with recognized standards such as REDcert2 and ISCC PLUS
Chemical recycling can be used to process plastic waste that is not mechanically recycled for technological or environmental reasons. While sorted single-variety waste fractions is to be recycled mechanically, chemical recycling can be used for mixed plastic waste - for example consisting of PE, PP, PS - for which further sorting is not economical.
Solution-oriented: Chemical recycling is an important addition to the recycling landscape. Changing the design of plastic products to make them mechanically recyclable is not always practical (for example, if it would degrade product properties or increase material consumption).
Virgin-quality products: In chemical recycling, plastic waste is converted back into raw materials for the chemical industry and allocated to products manufactured in BASF’s production Verbund using a mass balance method. These products have the same properties as products manufactured from fossil raw materials.
Easy to use: Our customers can process these products in the same way as conventionally manufactured products and use them in applications with high quality, hygiene, and performance requirements. These include medical applications, food packaging, and safety-related automotive parts. This helps to achieve higher recyclate use rates for products with the highest quality standards.
Transparently certified: Both the mass balance method, by which the proportion of recycled raw material is allocated to the product, and the products themselves are certified by independent auditors.
Conserves resources and reduces emissions: By using recycled raw materials, we can save fossil resources. In addition, products manufactured with chemically recycled raw materials using a mass balance approach release fewer greenhouse gases than conventional products made from primary fossil resources. This is because the plastic waste is not incinerated but used to make new chemical products.
Stay up to date: subscribe to our Sustainability Newsletter
What else is included in our sustainability promise? Lupranat ZERO, BMBCertTM, Plastics Hub