Wir unterstützen Sie dabei, Ihre Nachhaltigkeitsziele mit unseren kohlenstoffarmen Ammoniakprodukten zu erreichen.
Monomers
Chemikalien auf Ammoniakbasis
Portfolio
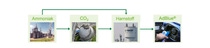
Ammoniak
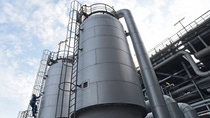
Ammoniak-Produktionsanlage in Ludwigshafen
Ammoniak ist eine der meistproduzierten Chemikalien der Welt mit einer weltweiten Jahreskapazität von 235 Millionen Tonnen. Mit der Erfindung des Ammoniakverfahrens durch BASF im Jahr 1913 wurde der Grundstein für diese Erfolgsgeschichte gelegt. Industrielles Ammoniak ist der Ausgangspunkt der modernen Landwirtschaft sowie vieler petrochemischer Wertschöpfungsketten. Die farblose Substanz ist bei Raumtemperatur gasförmig und hat einen charakteristischen stechenden Geruch, der so stark ist, dass der Mensch ihn schon in geringsten Konzentrationen wahrnehmen kann.
Die Hauptanwendung für Ammoniak bei BASF ist Harnstoff, der aus Ammoniak und Kohlendioxid unter hohem Druck hergestellt werden kann. Zudem ist Ammoniak ein wichtiger Rohstoff für viele andere Wertschöpfungsketten wie Salpetersäure, Amine und Isocyanate.
BASF vertreibt Ammoniak wasserfrei über Pipelines, Binnenschiffe und in Eisenbahnwaggons. BASF bietet auch Ammoniaklösung 24,5% in Eisenbahnwaggons und Tankwagen an.
Harnstoff
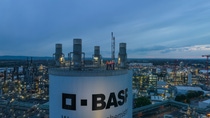
Prillturm - Teil der Harnstoffanlage
Vor mehr als 100 Jahren entwickelte BASF die weltweit erste industrielle Harnstoffproduktion. Heute ist Harnstoff einer der wichtigsten Rohstoffe in der chemischen Industrie. Er wird in einer Vielzahl von Produktionsverfahren eingesetzt und wird seit 1922 am Standort Ludwigshafen hergestellt.
Harnstoff kann auf vielfältige Weise eingesetzt werden. So wird er zum Beispiel bei der Herstellung von Leimen, Tränkharzen und Düngemitteln verwendet, aber auch als Bestandteil bestimmter kosmetischer Produkte und Medikamente. Außerdem wird es zur Herstellung von AdBlue®, dem Zusatzstoff für Dieselmotoren, verwendet.
Typische Abnehmerbranchen sind die Kosmetik- und Pharmaindustrie sowie die Hersteller von Harnstofflösungen. BASF vertreibt Harnstoffprills in Big Bags oder als Bulkware sowie Harnstofflösungen als Bulkware.
Flüssiges CO2
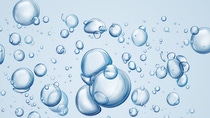
Flüssiges CO2
In Ludwigshafen verflüssigt die BASF einen Teil des CO2, das bei der Ammoniakproduktion entsteht. Kohlendioxid ist nicht brennbar, farblos und geruchlos.
Die Kunden der BASF verwenden das Kohlendioxid für die Herstellung von: Getränken, zum Zerkleinern, Dosieren, Abfüllen und Verpacken von Lebensmitteln, für Extraktionszwecke, zum Isolieren oder Entfernen von Aromastoffen aus Naturstoffen und für die Herstellung von Trockeneis und Pellets.
Die BASF vertreibt flüssiges CO2 (LCO2 3.0) in Lastwagen und Eisenbahnwaggons.
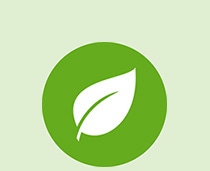
BASF bietet bietet nun Produkte mit reduziertem CO2-Fußabdruck für ihr Ammoniak- und Harnstoffportfolio an.
Ammoniak-Produktion bei BASF
Seit mehr als 100 Jahren ist Ammoniak ein unverzichtbarer Bestandteil des Produktionsverbundes. Die BASF hat eine weltweite Kapazität von 1,4 Millionen Tonnen Ammoniak.
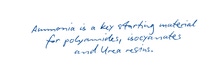
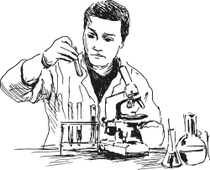
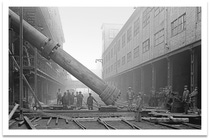
Die Anfänge
Im September 1913 wurde in Ludwigshafen die erste Anlage zur großtechnischen Herstellung von Ammoniak bei der BASF in Betrieb genommen. Die Ammoniaksynthese wurde erst durch das Haber-Bosch-Verfahren möglich.
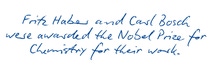
Die Optimierung zur Ressourceneffizienz beginnt
1922 baute BASF in Ludwigshafen die erste Harnstoffanlage der Welt. Harnstoff wurde zunächst zur Stickstoffdüngung, bald aber auch zur Herstellung von Holzleim eingesetzt.
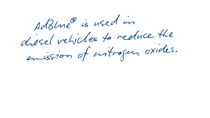
Ausbau einer erfolgreichen Technologie
In den späten 1960er Jahren wurden die Melamin- und die CO2-Verflüssigungsanlage gebaut. Im Jahr 2004 wurde das Portfolio erweitert, als BASF in Ludwigshafen die AdBlue®-Produktion aufnahm. AdBlue® ist eine vom Verband der Automobilindustrie (VDA) weltweit lizenzierte Marke für eine wässrige Lösung, die aus 32,5 % Harnstoff und entmineralisiertem Wasser besteht.
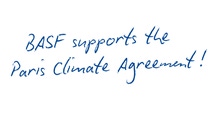
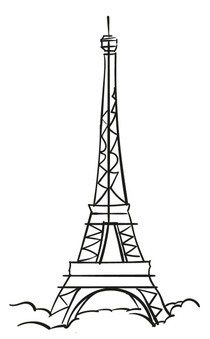
2015 – Ein wegweisendes Abkommen
Das Pariser Klimaabkommen ist ein internationales Abkommen, das 2015 von fast allen Staaten angenommen wurde, um den Klimawandel und seine negativen Auswirkungen zu bekämpfen. Ziel des Abkommens ist es, die weltweiten Treibhausgasemissionen deutlich zu reduzieren.
Im Jahr 2021 stellte BASF ihren Fahrplan zur Klimaneutralität vor
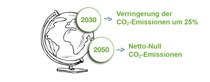
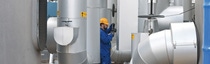